If you want your customers to have the best possible growing climate, and products that perform flawlessly in that climate, you’d better be into research and development. And you’re going to need a weather machinist.
For Behind the Screens, I met with Niclas Bergh-Gustafsson, Support Engineer in the nine-person R&D department at Kinna in Sweden, writes Tim Wright, staff writer at Svensson in Kinna. His job is to simulate extreme weather and speed up time. Watch him make weather here.
“We’re a team that run the weather machines at the lab,” he explains. “Our screens and nets are in use all over the world in all kinds of environments and our job is to understand how they can perform better and for longer in some pretty harsh places.”
Niclas explains that when Svensson created its first climate screens at the start of the 1970s it became clear that material science and in-house research and development were going to be critical to providing the quality guarantee the company stood for.
Screens and nets have to deal with tough conditions. Users of sunglasses or sunscreen may know that bright sunshine can damage the human eye and our skin. That’s because beyond the color violet, the sun’s light can corrode natural and man-made polymers.
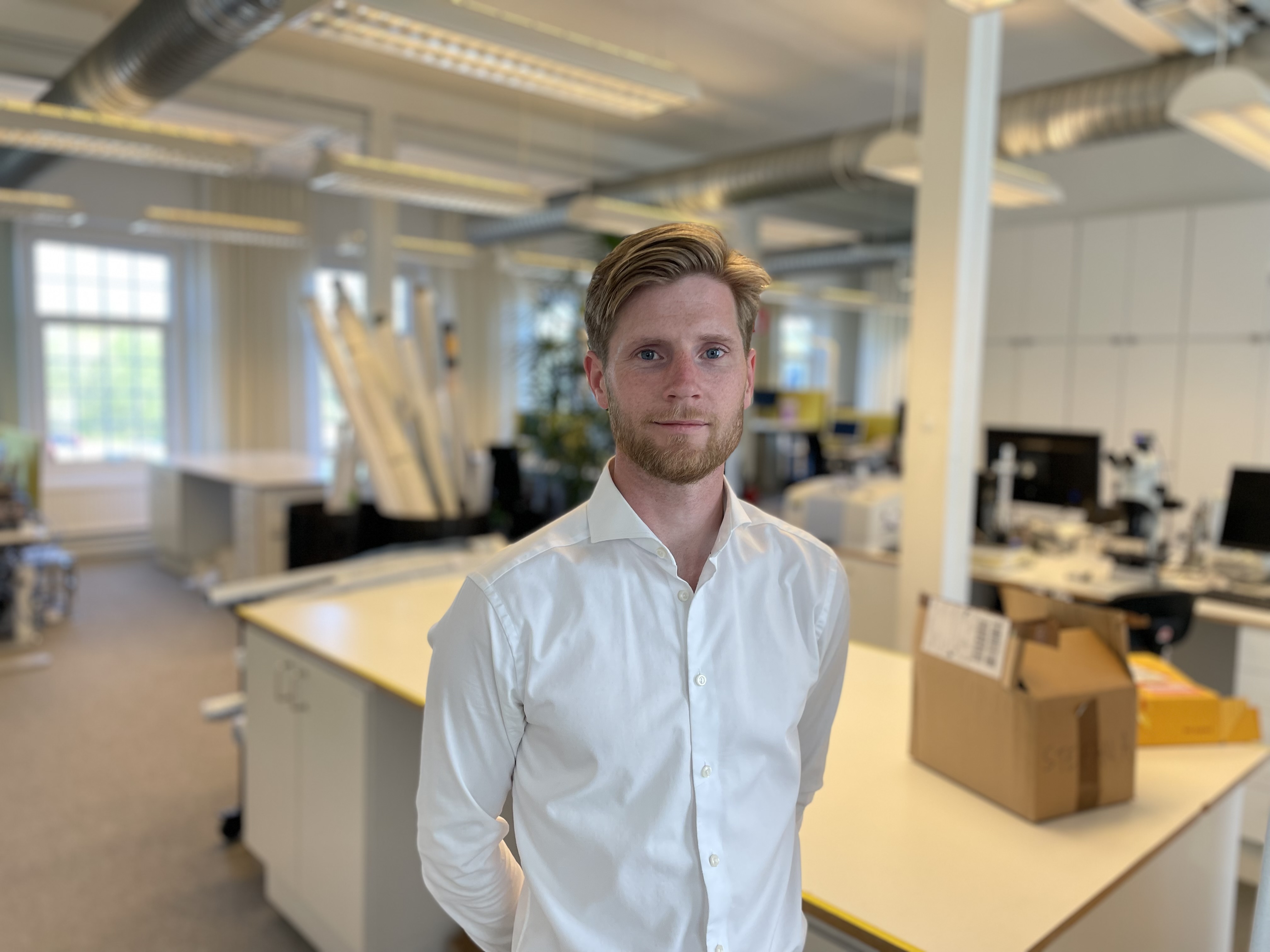
"I studied Textile Product Development and Entrepreneurship and I’m a bit of a tech nerd," says Niclas Bergh-Gustafsson in Research and Development at Svensson
The two long strands in the double helix of human and plant DNA are polymers and are vulnerable to damage from the more energetic Ultra Violet B (UVB) light. But so were some of the early materials Svensson knitted into its first products.
“We realized that we need to think of everything, and test everything,” Niclas explains. “That’s how we learned to take control of our supply chain, specify exactly the kinds of components that we use, and how we began to understand how to achieve best-in-class light transmission,” he adds.
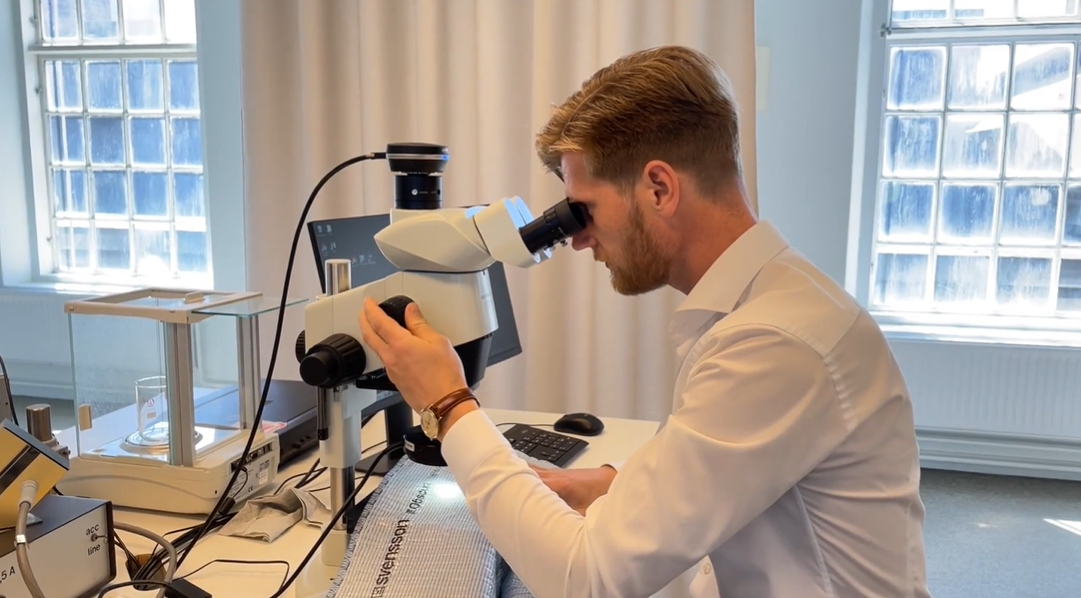
That’s how we learned to take control of our supply chain, specify exactly the kinds of components that we use, and how we began to understand how to achieve best-in-class light transmission
While real-world tests are carried out in the deserts and coastal plains of North America, up to 168 samples of shade cloth, insect net or energy and blackout screen take their turn in the artificial sun at the R&D lab in Kinna. Heat and humidity are simulated during an accelerated yearly cycle.
“We’re not done there,” adds Niclas. “We have machines that expose the samples to the light spectrum, and it’s very important to test the mechanical properties when the samples emerge,” he says.
Shrink tests are carried out. Stretch tests stress the screens tens of thousands of times.
But Niclas’s favorite instrument is the microscope.
“I studied Textile Product Development and Entrepreneurship and I’m a bit of a tech nerd,” he explains. “My grandmother and my aunt both worked with textiles here in Kinna. It’s long been our daily bread in this part of Sweden. Textiles are what we do.
“My first job at 20 was in weaving and I just have this passion for holding and feeling a textile, but I wanted to combine it with technology and entrepreneurship,” he adds.
“We’ve had this particular microscope for just a few months,” he says. “It’s really a beautiful instrument. When the materials come from all the simulators, it is as if we can visually dissect the surface of the fibers and inspect the monofilaments.”