All forms of production result in residual material. Reducing and minimising such material is among our responsibilities as a manufacturer, however it is inevitable that offcuts are created in connection with industrial weaving. We are therefore proud and thrilled to have found a solution to this problem in collaboration with The Loop Factory.
Weaving cloth on a mechanical loom results in offcuts, i.e. material that is cut away from the finished cloth product. On average, this amounts to around 2-4 percent per running metre of cloth depending on the quality of the covering. In the past, we have had projects to recycle residual material in wool, and in collaboration with The Loop Factory, we’ve now found a use for polyester off-cuts.
“With our current production, we generate around a couple of tonnes of polyester offcuts per year. These are quantities that are high enough to be of interest to other industrial actors, allowing us to create a new value chain. It’s impossible for us to reduce the waste generated in the process any further, and our goal has therefore always been to find a utility for that waste. And that’s what we’ve accomplished now,” said Louise Holgersson, product developer at Svensson.
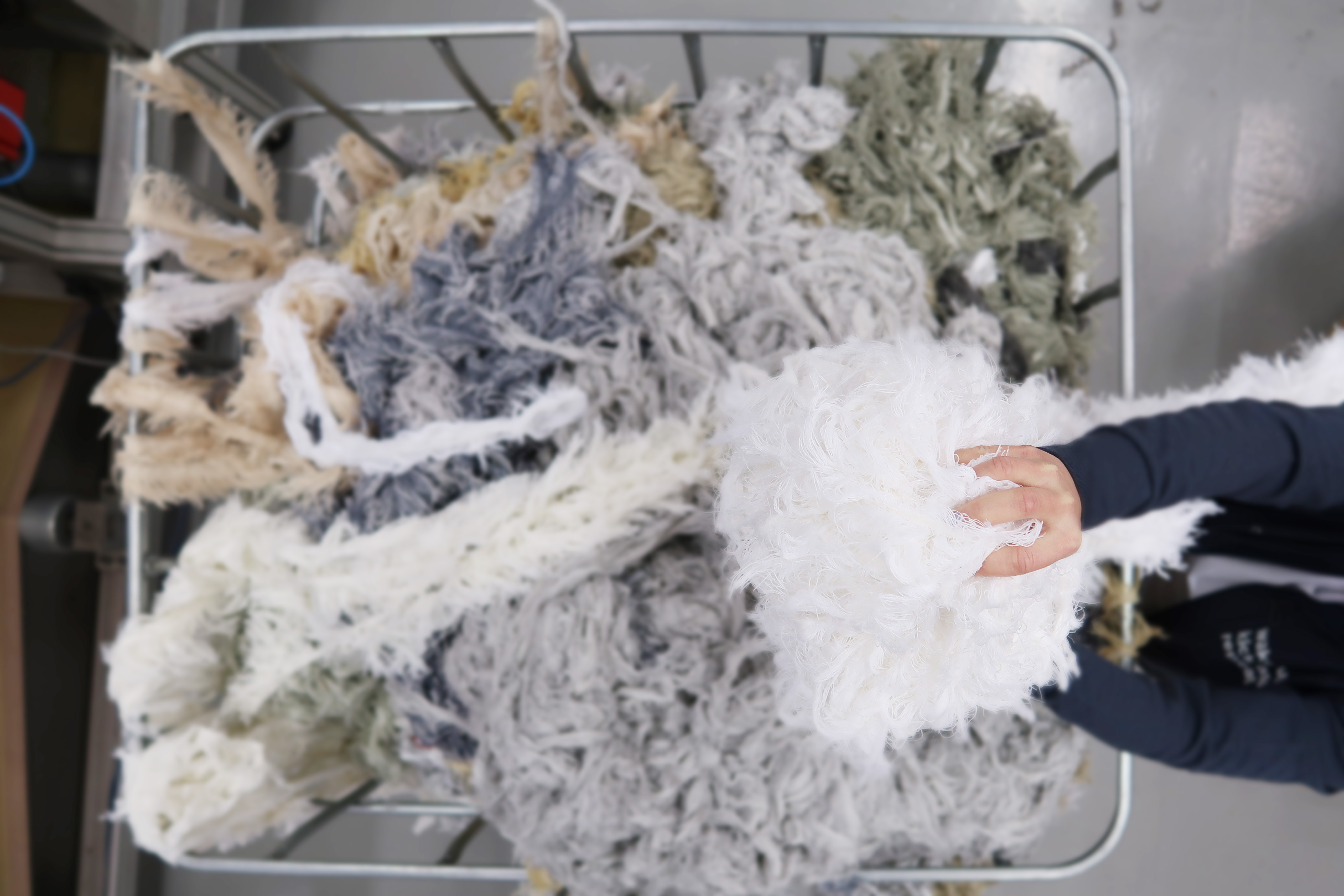
The Loop Factory is an innovation hub that develops new products from residual material to create circular business models involving multiple parties. The material which is being used now exclusively stems from offcuts.
“A positive aspect of using leftover textile material is that the material is completely unused and possesses the same qualities of the cloth itself. We know exactly what it contains, where it’s been sourced from, which certifications it lives up to and the social impact that the manufacturer contributes towards. That’s the recipe for achieving a circular system,” said Pontus Törnqvist, circular designer at The Loop Factory. “Svensson’s history and amazing woven products have made this project even more fun,” he added. “Together with Svensson, we had the conditions to create a unique product that’s made in Sweden based on residual material and with short transport distances.”
Our ambition is to ensure that all material that we produce ends up being used for something. In parallel to a growing worldwide interest in sustainability, a wholly separate interest in circular raw materials has also emerged. This has created conditions for finding value chains that benefit every segment of the chain.
“It’s been a challenge to come up with a usable end product in the past,” said Holgersson. “But I feel like this is just the start, and I see an entirely different future now for our residual material in other products as well.”
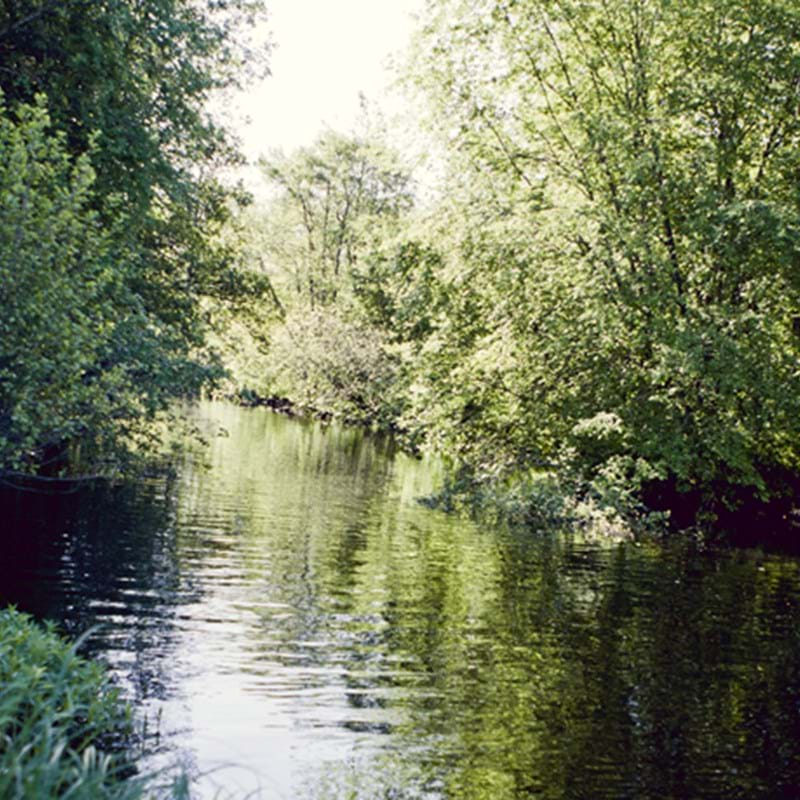
Sustainability for Svensson
By setting strict requirements on raw materials and by owning the entire manufacturing process, we control the entire production chain from the yarn used to the finished product. That means we know what it contains and what characteristics it has.
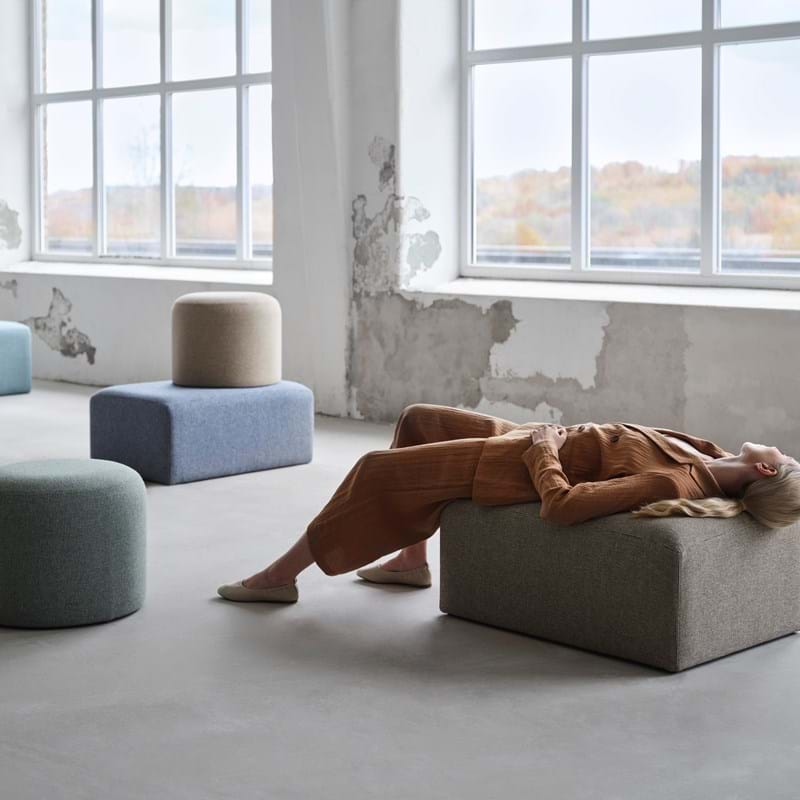
Debut - a sustainable upholstery fabric
Waste materials from the Ramie production are sent back to our spinner on the same truck that just delivered yarn to us. Then it’s torn up and spun into new yarn before coming back to the factory to be woven into Debut.
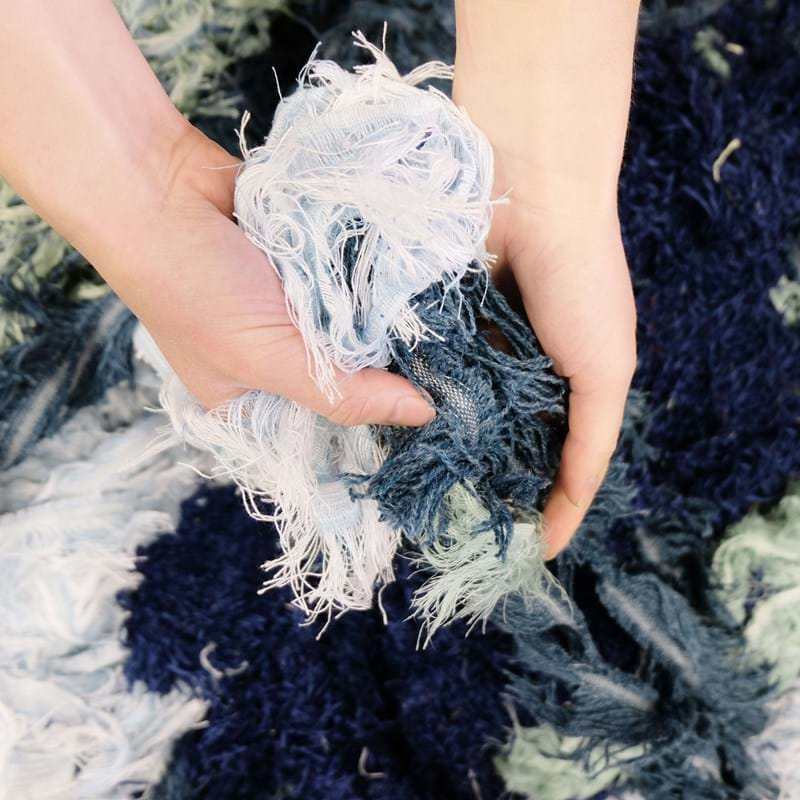
Loop Factory
The Loop Factory offers a platform for successful sustainable innovations, from idea to commercialization. They are dedicated to creating a more sustainable future, where professional skills, lab and networks are utilized to make a change.